INNERGY vs DBA Manufacturing
Last Updated:Our analysts compared INNERGY vs DBA Manufacturing based on data from our 400+ point analysis of Manufacturing Software, user reviews and our own crowdsourced data from our free software selection platform.
Product Basics
INNERGY is a sophisticated software solution designed to streamline and optimize manufacturing operations through its comprehensive ERP capabilities. It is particularly well-suited for mid-sized to large manufacturing firms seeking to enhance efficiency, reduce costs, and improve overall productivity. The software excels in managing complex tasks such as inventory control, production scheduling, and supply chain management, making it an invaluable tool for companies with intricate manufacturing processes.
Users appreciate INNERGY for its intuitive interface and robust feature set, which includes real-time data analytics, customizable reporting, and seamless integration with existing systems. The software's ability to provide actionable insights and facilitate informed decision-making is frequently highlighted as a significant benefit. Additionally, INNERGY's scalability ensures it can grow alongside a business, adapting to evolving needs.
Pricing for INNERGY typically falls within a mid-to-high range, often based on the number of users and specific modules required, with options for monthly or annual payments. Compared to similar products, INNERGY is praised for its reliability and comprehensive support, making it a preferred choice for many in the manufacturing sector.
DBA Manufacturing is a comprehensive software solution designed to streamline and manage various manufacturing tasks. It is particularly well-suited for small to mid-sized manufacturing companies across diverse industries such as electronics, machinery, and consumer goods. The software excels in providing robust inventory control, production scheduling, and job costing capabilities, making it an invaluable tool for businesses looking to enhance operational efficiency and reduce costs.
One of the standout benefits of DBA Manufacturing is its ability to integrate seamlessly with existing systems, offering a user-friendly interface that simplifies complex manufacturing processes. Popular features include real-time inventory tracking, detailed production planning, and comprehensive reporting tools. These features empower manufacturers to make informed decisions, optimize resource allocation, and improve overall productivity.
Compared to similar products, DBA Manufacturing is often praised for its affordability and ease of use. While specific pricing details are not readily available, it is recommended that users contact SelectHub for a tailored pricing quote based on their unique requirements. This ensures that businesses receive a solution that fits their budget and operational needs.
Product Assistance
Product Insights
- Improved Efficiency: Streamlines production processes by automating routine tasks, reducing manual errors and saving time.
- Enhanced Visibility: Provides real-time data on inventory levels, production status, and order tracking, enabling better decision-making.
- Cost Reduction: Identifies waste and inefficiencies in the manufacturing process, helping to lower operational costs.
- Better Resource Management: Optimizes the use of materials, labor, and machinery, ensuring resources are used effectively.
- Scalability: Easily adapts to the growing needs of your business, supporting expansion without significant additional investment.
- Regulatory Compliance: Helps maintain compliance with industry standards and regulations by providing accurate and timely documentation.
- Customer Satisfaction: Improves order accuracy and delivery times, leading to higher customer satisfaction and loyalty.
- Data-Driven Insights: Offers comprehensive analytics and reporting tools to identify trends and make informed strategic decisions.
- Integration Capabilities: Seamlessly integrates with other business systems, such as CRM and accounting software, for a unified workflow.
- Enhanced Collaboration: Facilitates better communication and collaboration among different departments, ensuring everyone is on the same page.
- Inventory Optimization: Maintains optimal inventory levels by predicting demand and managing stock efficiently.
- Quality Control: Monitors production quality in real-time, allowing for immediate corrective actions and maintaining high standards.
- Reduced Downtime: Schedules maintenance and predicts equipment failures, minimizing unexpected downtime and production delays.
- Customizable Workflows: Allows for the customization of workflows to match specific business processes, enhancing operational flexibility.
- Employee Productivity: Empowers employees with the tools and information they need to perform their tasks more effectively.
- Improved Production Efficiency: Streamlines workflows and reduces bottlenecks, leading to faster production times and higher throughput.
- Enhanced Inventory Management: Provides real-time tracking of inventory levels, minimizing stockouts and overstock situations.
- Cost Reduction: Optimizes resource allocation and reduces waste, leading to significant cost savings in materials and labor.
- Accurate Demand Forecasting: Utilizes historical data and trends to predict future demand, ensuring better planning and resource allocation.
- Quality Control: Implements rigorous quality checks at various stages of production, ensuring consistent product quality and reducing defects.
- Scalability: Easily adapts to the growing needs of your business, supporting expansion without requiring significant changes to the system.
- Regulatory Compliance: Helps maintain compliance with industry standards and regulations through automated documentation and reporting.
- Enhanced Collaboration: Facilitates better communication and coordination among different departments, leading to more cohesive operations.
- Data-Driven Decision Making: Provides comprehensive analytics and reporting tools, enabling informed decisions based on real-time data.
- Customer Satisfaction: Improves order accuracy and delivery times, leading to higher customer satisfaction and loyalty.
- Reduced Lead Times: Streamlines the production process, significantly cutting down on lead times from order to delivery.
- Resource Optimization: Ensures optimal use of machinery and labor, maximizing productivity and minimizing downtime.
- Flexibility in Production: Allows for easy adjustments to production schedules and processes to meet changing market demands.
- Comprehensive Traceability: Tracks every component and process step, providing full traceability for quality assurance and recall management.
- Integration Capabilities: Seamlessly integrates with other business systems, such as ERP and CRM, for a unified operational approach.
- Real-Time Data Analytics: Provides up-to-the-minute insights into production metrics, inventory levels, and financial performance.
- Customizable Dashboards: Allows users to tailor their interface to display the most relevant data for their specific role or department.
- Advanced Inventory Management: Tracks raw materials, work-in-progress, and finished goods with precision, reducing waste and optimizing stock levels.
- Production Scheduling: Facilitates efficient planning and scheduling of manufacturing processes to maximize throughput and minimize downtime.
- Quality Control Integration: Embeds quality checks and compliance tracking directly into the production workflow, ensuring consistent product standards.
- Supply Chain Management: Enhances visibility and coordination across the entire supply chain, from procurement to delivery.
- Financial Management: Integrates accounting functions such as accounts payable, receivable, and general ledger, streamlining financial operations.
- Human Resources Module: Manages employee records, payroll, and performance evaluations within the same system.
- Customer Relationship Management (CRM): Tracks customer interactions, sales orders, and service requests to improve customer satisfaction and retention.
- Mobile Access: Enables users to access critical ERP functions from smartphones and tablets, ensuring flexibility and responsiveness.
- Compliance and Reporting: Generates detailed reports to meet industry-specific regulatory requirements and internal audit needs.
- Scalability: Adapts to the growing needs of a business, whether expanding production lines or entering new markets.
- Integration Capabilities: Seamlessly connects with other enterprise systems such as CRM, SCM, and PLM for a unified IT ecosystem.
- Role-Based Access Control: Ensures data security by allowing administrators to define user permissions based on job roles.
- Automated Workflows: Streamlines repetitive tasks and processes, reducing manual intervention and increasing efficiency.
- Multi-Language and Multi-Currency Support: Facilitates global operations by supporting various languages and currencies.
- Document Management: Centralizes storage and retrieval of important documents, ensuring easy access and version control.
- Vendor Management: Tracks vendor performance, contracts, and communications to optimize procurement processes.
- Project Management: Provides tools for planning, executing, and monitoring projects, ensuring they stay on time and within budget.
- Training and Support: Offers comprehensive training resources and customer support to ensure successful implementation and ongoing use.
- Inventory Management: Comprehensive tools for tracking raw materials, work-in-progress, and finished goods.
- Bill of Materials (BOM): Detailed BOM management, allowing for multi-level BOMs and sub-assemblies.
- Shop Control: Real-time shop floor control with job tracking and work center scheduling.
- MRP (Material Requirements Planning): Automated MRP system to ensure materials are available for production and products are available for delivery.
- Job Costing: Accurate job costing capabilities to track labor, materials, and overhead costs for each job.
- Sales Order Management: Efficient handling of sales orders from entry to fulfillment, including backorder management.
- Purchase Order Management: Streamlined purchase order processing with vendor management and order tracking.
- Production Scheduling: Advanced scheduling tools to optimize production workflows and minimize downtime.
- Quality Control: Integrated quality control processes to ensure product standards are met consistently.
- Reporting and Analytics: Robust reporting and analytics tools for data-driven decision-making and performance monitoring.
- Barcode Scanning: Support for barcode scanning to improve accuracy and efficiency in inventory and production processes.
- Multi-Currency Support: Capability to handle transactions in multiple currencies, ideal for global operations.
- Customer Relationship Management (CRM): Built-in CRM features to manage customer interactions and improve service.
- Document Management: Centralized document management system for easy access to important files and records.
- Integration Capabilities: Seamless integration with other business systems and software for enhanced functionality.
- User Permissions: Granular user permissions to control access to sensitive information and functions.
- Mobile Access: Mobile-friendly interface for accessing the system on-the-go.
- Customizable Dashboards: Personalized dashboards to display key metrics and information relevant to individual users.
- Scalability: Scalable architecture to grow with your business needs.
Product Ranking
#74
among all
Manufacturing Software
#151
among all
Manufacturing Software
User Sentiment Summary
DBA Manufacturing has a 'excellent' User Satisfaction Rating of 90% when considering 10 user reviews from 2 recognized software review sites.
Awards
DBA Manufacturing stands above the rest by achieving an ‘Excellent’ rating as a User Favorite.
Synopsis of User Ratings and Reviews
User reviews paint a mixed picture of the software, with some praising its robust features while others lament its clunky interface and lack of customization. INNERGY's strength lies in its comprehensive suite of features, which cater to a wide range of manufacturing needs. Users appreciate its ability to manage everything from production planning and scheduling to inventory control and quality management. For example, one user highlighted how INNERGY's real-time inventory tracking helped them avoid costly stockouts and improve production efficiency. However, the software's user interface is often criticized for being outdated and difficult to navigate. Some users have complained about the lack of intuitive features and the steep learning curve, which can be a major hurdle for new users. Additionally, INNERGY's customization options are limited, making it difficult for businesses to tailor the software to their specific needs. One user expressed frustration with the lack of flexibility in customizing reports, which made it challenging to get the specific data they needed. Despite these drawbacks, INNERGY remains a popular choice for businesses that require a comprehensive manufacturing ERP solution. It is particularly well-suited for large enterprises with complex manufacturing processes and a need for robust data management capabilities. However, smaller businesses or those with limited IT resources may find the software's complexity and lack of customization options to be a significant barrier.
Is DBA Manufacturing all its cracked up to be? User reviews from the past year paint a mixed picture, highlighting both its strengths and weaknesses. On the plus side, DBA Manufacturing is lauded for its comprehensive suite of features, encompassing inventory control, bill of materials management, production planning, and shop floor control. This makes it a valuable tool for small and mid-sized manufacturers seeking to streamline their operations. However, a significant drawback is the system's reliance on manual MRP updates. This means production data isn't live and must be entered after the fact, which can be a pain point for some users. This aspect sets it apart from more automated solutions available in the market. Despite this limitation, DBA Manufacturing's strength lies in its user-friendliness and focus on the needs of smaller businesses. The software's training, conducted using a sample company, ensures minimal disruption to live operations. This is particularly beneficial for businesses transitioning from less sophisticated systems. In conclusion, DBA Manufacturing is best suited for small to mid-sized manufacturers who prioritize a comprehensive feature set and ease of use over real-time data updates. Its focus on core manufacturing functions and accessible learning curve makes it a viable option for businesses looking to dip their toes into the world of MRP without feeling overwhelmed.
Screenshots
Top Alternatives in Manufacturing Software

Acumatica
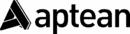
Aptean ERP

Cetec ERP

DELMIAworks
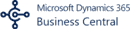
Dynamics 365 Business Central

Dynamics 365 SCM

Epicor Kinetic
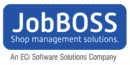
JobBOSS²
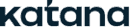
Katana MRP
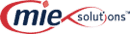
MIE Trak Pro

MRPEasy
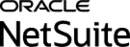
NetSuite
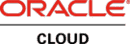
Oracle Fusion Cloud

Plex Systems

Sage 100 Cloud

SAP S/4HANA Cloud

SYSPRO
SyteLine
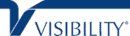
Visibility ERP
FAQ
We’re the employee-owned Austin-based startup democratizing software data so you can make your decisions in an influence-free zone. Our market data is crowdsourced from our user-base of 100,000+ companies.
WE DISTILL IT INTO REAL REQUIREMENTS, COMPARISON REPORTS, PRICE GUIDES and more...

