Simio vs INNERGY
Last Updated:Our analysts compared Simio vs INNERGY based on data from our 400+ point analysis of Manufacturing Software, user reviews and our own crowdsourced data from our free software selection platform.
Product Basics
INNERGY is a sophisticated software solution designed to streamline and optimize manufacturing operations through its comprehensive ERP capabilities. It is particularly well-suited for mid-sized to large manufacturing firms seeking to enhance efficiency, reduce costs, and improve overall productivity. The software excels in managing complex tasks such as inventory control, production scheduling, and supply chain management, making it an invaluable tool for companies with intricate manufacturing processes.
Users appreciate INNERGY for its intuitive interface and robust feature set, which includes real-time data analytics, customizable reporting, and seamless integration with existing systems. The software's ability to provide actionable insights and facilitate informed decision-making is frequently highlighted as a significant benefit. Additionally, INNERGY's scalability ensures it can grow alongside a business, adapting to evolving needs.
Pricing for INNERGY typically falls within a mid-to-high range, often based on the number of users and specific modules required, with options for monthly or annual payments. Compared to similar products, INNERGY is praised for its reliability and comprehensive support, making it a preferred choice for many in the manufacturing sector.
Product Assistance
Product Insights
- Easy Learning Curve: Leverage Simio's tools to create models whether users are experienced or not.
- Single Model: Work with one model no matter if it's large or intricate rather than working with individual parts.
- Realistic Models: Make models realistic and test them in various atmospheres and scenarios.
- Interactive Workpieces: Create "intelligent" workpieces that communicate with each other, enabling detached yet continuous systems.
- Improved Efficiency: Streamlines production processes by automating routine tasks, reducing manual errors and saving time.
- Enhanced Visibility: Provides real-time data on inventory levels, production status, and order tracking, enabling better decision-making.
- Cost Reduction: Identifies waste and inefficiencies in the manufacturing process, helping to lower operational costs.
- Better Resource Management: Optimizes the use of materials, labor, and machinery, ensuring resources are used effectively.
- Scalability: Easily adapts to the growing needs of your business, supporting expansion without significant additional investment.
- Regulatory Compliance: Helps maintain compliance with industry standards and regulations by providing accurate and timely documentation.
- Customer Satisfaction: Improves order accuracy and delivery times, leading to higher customer satisfaction and loyalty.
- Data-Driven Insights: Offers comprehensive analytics and reporting tools to identify trends and make informed strategic decisions.
- Integration Capabilities: Seamlessly integrates with other business systems, such as CRM and accounting software, for a unified workflow.
- Enhanced Collaboration: Facilitates better communication and collaboration among different departments, ensuring everyone is on the same page.
- Inventory Optimization: Maintains optimal inventory levels by predicting demand and managing stock efficiently.
- Quality Control: Monitors production quality in real-time, allowing for immediate corrective actions and maintaining high standards.
- Reduced Downtime: Schedules maintenance and predicts equipment failures, minimizing unexpected downtime and production delays.
- Customizable Workflows: Allows for the customization of workflows to match specific business processes, enhancing operational flexibility.
- Employee Productivity: Empowers employees with the tools and information they need to perform their tasks more effectively.
- Agent-Based Modeling and Simulation: Integrate data from enterprise relationship solutions, customer relationship systems and other databanks to produce effective simulation models that obtain through results due to this capability.
- Discrete Event Modeling and Simulation: Work with a library of stationary workpieces and tools in addition to stimulating workflows and integrating custom models that represent shop floor resources via this attribute.
- Continuous Simulation and Modeling: Integrate real-time and previous data from process workflows, supply chains and material flow to understand shop floor procedures with this tool's data analytics tool.
- 3D Object-Based Modeling: Craft graphic models step by step and swiftly make objects via the 3D object-based modeling apparatus.
- Numerous Modeling: Manage multiple standard and "intelligent" objects that can interact with each other with various modeling functionalities.
- Optimal Scheduling: Initiate models to perform risk-based ideal scheduling via this feature
- Real-Time Data Analytics: Provides up-to-the-minute insights into production metrics, inventory levels, and financial performance.
- Customizable Dashboards: Allows users to tailor their interface to display the most relevant data for their specific role or department.
- Advanced Inventory Management: Tracks raw materials, work-in-progress, and finished goods with precision, reducing waste and optimizing stock levels.
- Production Scheduling: Facilitates efficient planning and scheduling of manufacturing processes to maximize throughput and minimize downtime.
- Quality Control Integration: Embeds quality checks and compliance tracking directly into the production workflow, ensuring consistent product standards.
- Supply Chain Management: Enhances visibility and coordination across the entire supply chain, from procurement to delivery.
- Financial Management: Integrates accounting functions such as accounts payable, receivable, and general ledger, streamlining financial operations.
- Human Resources Module: Manages employee records, payroll, and performance evaluations within the same system.
- Customer Relationship Management (CRM): Tracks customer interactions, sales orders, and service requests to improve customer satisfaction and retention.
- Mobile Access: Enables users to access critical ERP functions from smartphones and tablets, ensuring flexibility and responsiveness.
- Compliance and Reporting: Generates detailed reports to meet industry-specific regulatory requirements and internal audit needs.
- Scalability: Adapts to the growing needs of a business, whether expanding production lines or entering new markets.
- Integration Capabilities: Seamlessly connects with other enterprise systems such as CRM, SCM, and PLM for a unified IT ecosystem.
- Role-Based Access Control: Ensures data security by allowing administrators to define user permissions based on job roles.
- Automated Workflows: Streamlines repetitive tasks and processes, reducing manual intervention and increasing efficiency.
- Multi-Language and Multi-Currency Support: Facilitates global operations by supporting various languages and currencies.
- Document Management: Centralizes storage and retrieval of important documents, ensuring easy access and version control.
- Vendor Management: Tracks vendor performance, contracts, and communications to optimize procurement processes.
- Project Management: Provides tools for planning, executing, and monitoring projects, ensuring they stay on time and within budget.
- Training and Support: Offers comprehensive training resources and customer support to ensure successful implementation and ongoing use.
Product Ranking
#44
among all
Manufacturing Software
#74
among all
Manufacturing Software
User Sentiment Summary
Simio has a 'excellent' User Satisfaction Rating of 94% when considering 103 user reviews from 1 recognized software review sites.
Awards
Simio stands above the rest by achieving an ‘Excellent’ rating as a User Favorite.
Synopsis of User Ratings and Reviews
Simio is a powerful and versatile software known for its ability to manage a wide range of manufacturing tasks. Users praise its user-friendly interface and ability to generate accurate reports, finding it superior to other products in terms of ease of use and reporting capabilities. However, some users have reported a steep learning curve and unclear documentation, suggesting that Simio might require more upfront investment in training compared to competitors like AnyLogic or Arena. Despite these drawbacks, Simio is lauded for its object-oriented approach, which allows for more flexible and customizable modeling compared to traditional process-based simulation software. This makes it particularly well-suited for complex manufacturing environments where adaptability is key. While the software's pricing has been a point of contention for some, its robust features and positive user feedback position it as a valuable tool for manufacturing companies of all sizes. However, its complexity might make it more suitable for larger organizations with dedicated resources for training and implementation. Smaller companies with limited resources might find simpler, more affordable alternatives more appealing.
User reviews paint a mixed picture of the software, with some praising its robust features while others lament its clunky interface and lack of customization. INNERGY's strength lies in its comprehensive suite of features, which cater to a wide range of manufacturing needs. Users appreciate its ability to manage everything from production planning and scheduling to inventory control and quality management. For example, one user highlighted how INNERGY's real-time inventory tracking helped them avoid costly stockouts and improve production efficiency. However, the software's user interface is often criticized for being outdated and difficult to navigate. Some users have complained about the lack of intuitive features and the steep learning curve, which can be a major hurdle for new users. Additionally, INNERGY's customization options are limited, making it difficult for businesses to tailor the software to their specific needs. One user expressed frustration with the lack of flexibility in customizing reports, which made it challenging to get the specific data they needed. Despite these drawbacks, INNERGY remains a popular choice for businesses that require a comprehensive manufacturing ERP solution. It is particularly well-suited for large enterprises with complex manufacturing processes and a need for robust data management capabilities. However, smaller businesses or those with limited IT resources may find the software's complexity and lack of customization options to be a significant barrier.
Screenshots
Top Alternatives in Manufacturing Software

Acumatica
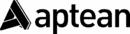
Aptean ERP

Cetec ERP

DELMIAworks
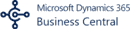
Dynamics 365 Business Central

Dynamics 365 SCM

Epicor Kinetic
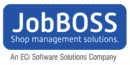
JobBOSS²
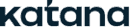
Katana MRP
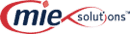
MIE Trak Pro

MRPEasy
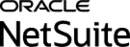
NetSuite
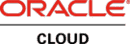
Oracle Fusion Cloud

Plex Systems

Sage 100 Cloud

SAP S/4HANA Cloud

SYSPRO
SyteLine
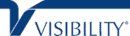
Visibility ERP
FAQ
We’re the employee-owned Austin-based startup democratizing software data so you can make your decisions in an influence-free zone. Our market data is crowdsourced from our user-base of 100,000+ companies.
WE DISTILL IT INTO REAL REQUIREMENTS, COMPARISON REPORTS, PRICE GUIDES and more...

